Case Study – Linx Printing Technologies (crimping)
The Challenge:
As part of a larger filling and sealing project Linx Printing Technologies asked Universal Filling Machine Company for a solution to seal septums onto a new design of ink and solvent cartridge. The critical requirements were:
- ATEX certified for use in a potentially explosive atmosphere (Zone 1)
- Septum must be sealed to be 100% leak-proof
- Crimp must be formed perfectly to allow the cartridge to be installed and removed easily
Products to fill:
- Aluminium Septums
- Plastic Ink Cartridges
The Solution:
Universal supplied Linx with a Coven AP02 semi-automatic crimping machine for initial crimping trials. Some redesign was needed on the neck of the plastic cartridge and to the length of the septum to achieve a perfect seal. Universal made bespoke plastic pucks to orientate the cartridge correctly during the crimping process. This simplified the changeover from one cartridge size to another.
Following successful trials on the semi-automatic machine, Linx Printing Technologies ordered a fully automatic filling and crimping solution which included:
- Rotary infeed table – special design to fit the small space & ATEX motor
- Posimatic EV automatic filling machine was designed with quick release interchangeable filling heads to allow rapid changeovers of the various liquids – this new design eliminated the need to clean as each ink had its own dedicated filling pump
- Vibratory bowl feeder with the ability to sort both plastic screw caps and aluminium septums
- Posicap cap tightening machine with two heads – one suitable for screw caps and the second for crimping. Each capping head had its own gating system and could be changed over from one to the other at the flick of a switch
- The three container sizes were handled in pucks in order to minimise downtime on changeover from one bottle to another.
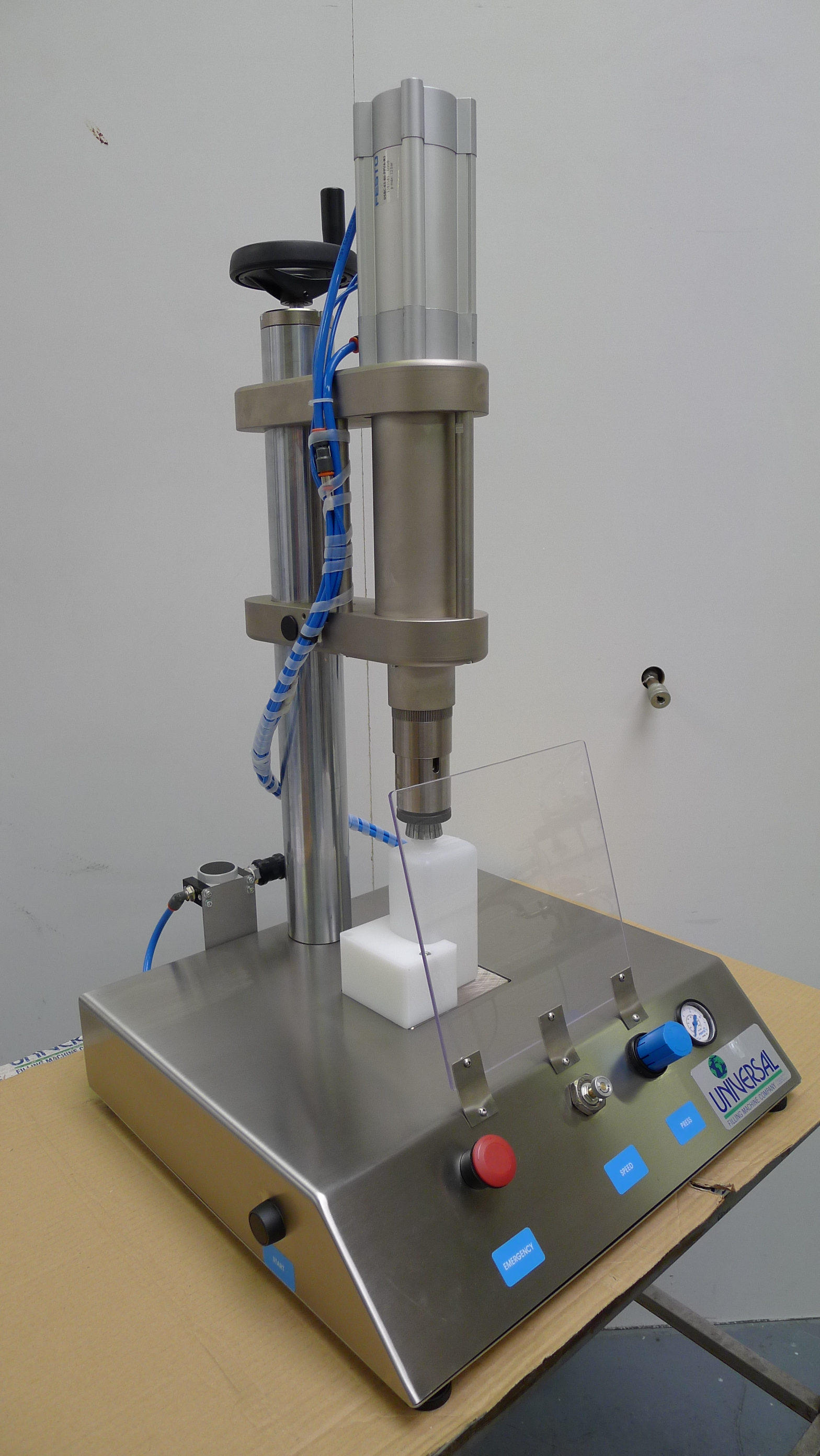