Two distinct filling technologies are available for semi-automatic and fully automatic filling machines: volumetric and vacuum-level filling.
Manually operated filling machines tend only to fill volumetrically.
Volumetric filling machines
Manual liquid filling machines use a piston within a cylinder to force liquid into the container.
These normally have a pneumatically powered pump mechanism, set to fill containers with the required volume of liquid, fed from either a floor-standing container or a machine-mounted hopper.
Containers are positioned below the filling nozzles and a foot pedal switch to start the filling process.
Volumes between 5ml and 25-litres can be handled by volumetric filling machines and up to 150 containers per minute can be filled, depending on the fill volume, liquid viscosity and level of machine automation.
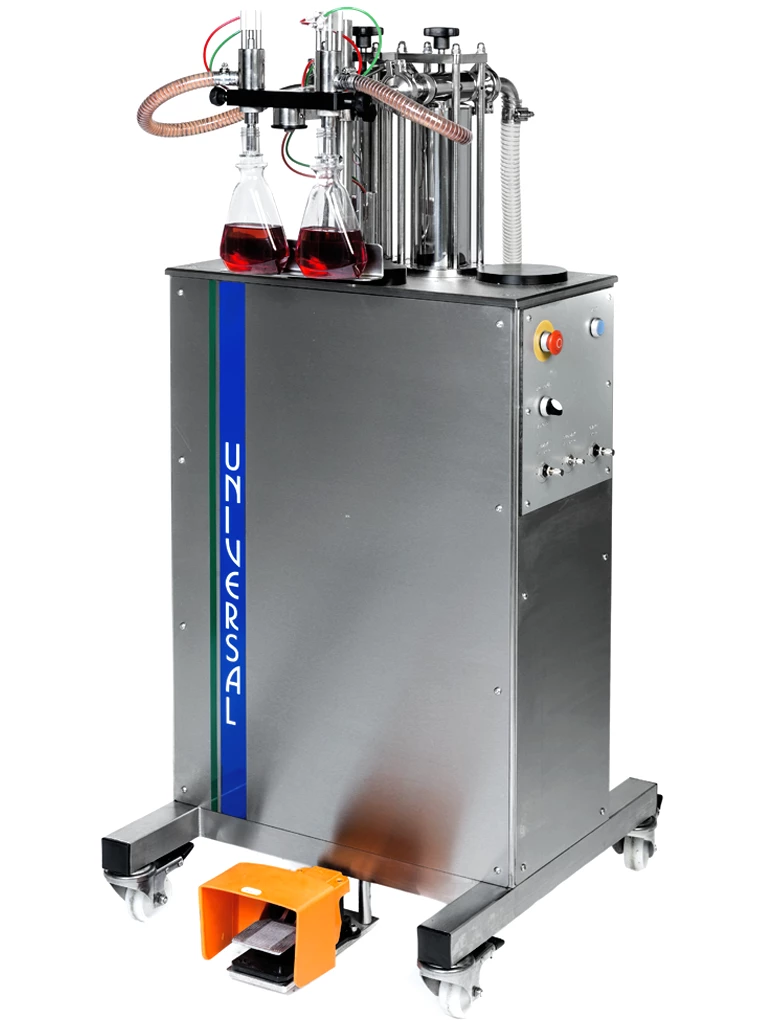
Vacuum level filling machines
Vacuum level semi-automatic filling machines use the rim at the top of the container to form an airtight seal around the filling nozzle.
This airtight seal creates a vacuum within the bottle which draws free-flowing liquids from a supply tank into the bottle, via specially designed nozzles. These nozzles have a small hole on the side which is connected to a small internal tube.
The height of this hole in relation to the top of the container during filling determines the level of liquid dispensed. The small hole in the nozzle scavenges excess liquid from the filling process and collects it in a receiver for reuse.
Vacuum level filling machines fill containers to the same height each time, rather than dispensing the same volume. This is particularly useful for glass bottles which will be side-by-side on display shelves in shops. Glass bottles vary in capacity quite a lot, yet vacuum-level filling ensures the level each bottle is filled to is the same, giving a consistent appearance from one bottle to the next. Vacuum level filling requires rigid containers which won’t collapse under a vacuum.
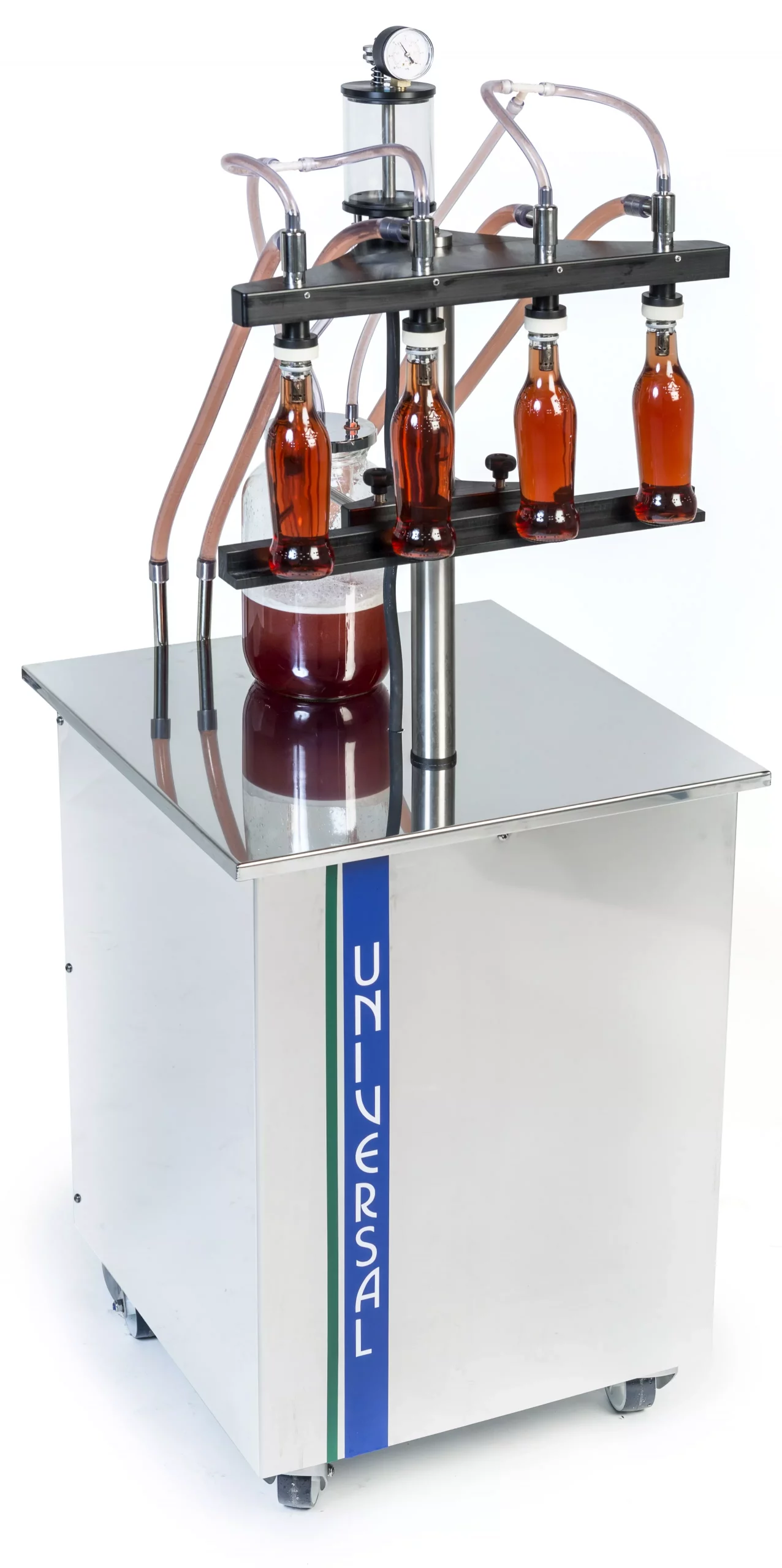
Vacuum-level machines have virtually no moving parts, making them incredibly reliable, and can fill up to 120 bottles per minute depending on the container type, number of filling heads and level of automation.
Bottles are simply positioned with their top in contact with a sealing ring around the nozzle. The container will start to fill as soon as an airtight seal is made and stop when the pre-determined fill height is reached.
Two distinct filling technologies are available for semi-automatic and fully automatic filling machines: volumetric and vacuum-level filling.
Manually operated filling machines tend only to fill volumetrically.
Volumetric filling machines
Manual liquid filling machines use a piston within a cylinder to force liquid into the container.
These normally have a pneumatically powered pump mechanism, set to fill containers with the required volume of liquid, fed from either a floor-standing container or a machine-mounted hopper.
Containers are positioned below the filling nozzles and a foot pedal switch to start the filling process.
Volumes between 5ml and 25-litres can be handled by volumetric filling machines and up to 150 containers per minute can be filled, depending on the fill volume, liquid viscosity and level of machine automation.
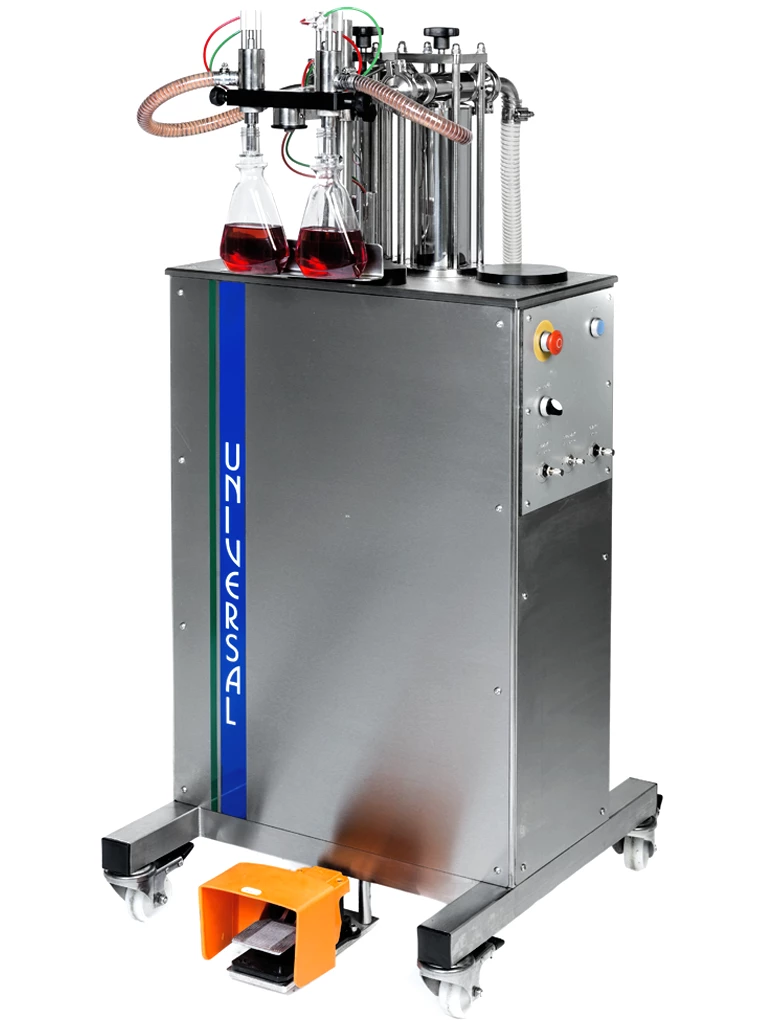
Vacuum level filling machines
Vacuum level semi-automatic filling machines use the rim at the top of the container to form an airtight seal around the filling nozzle.
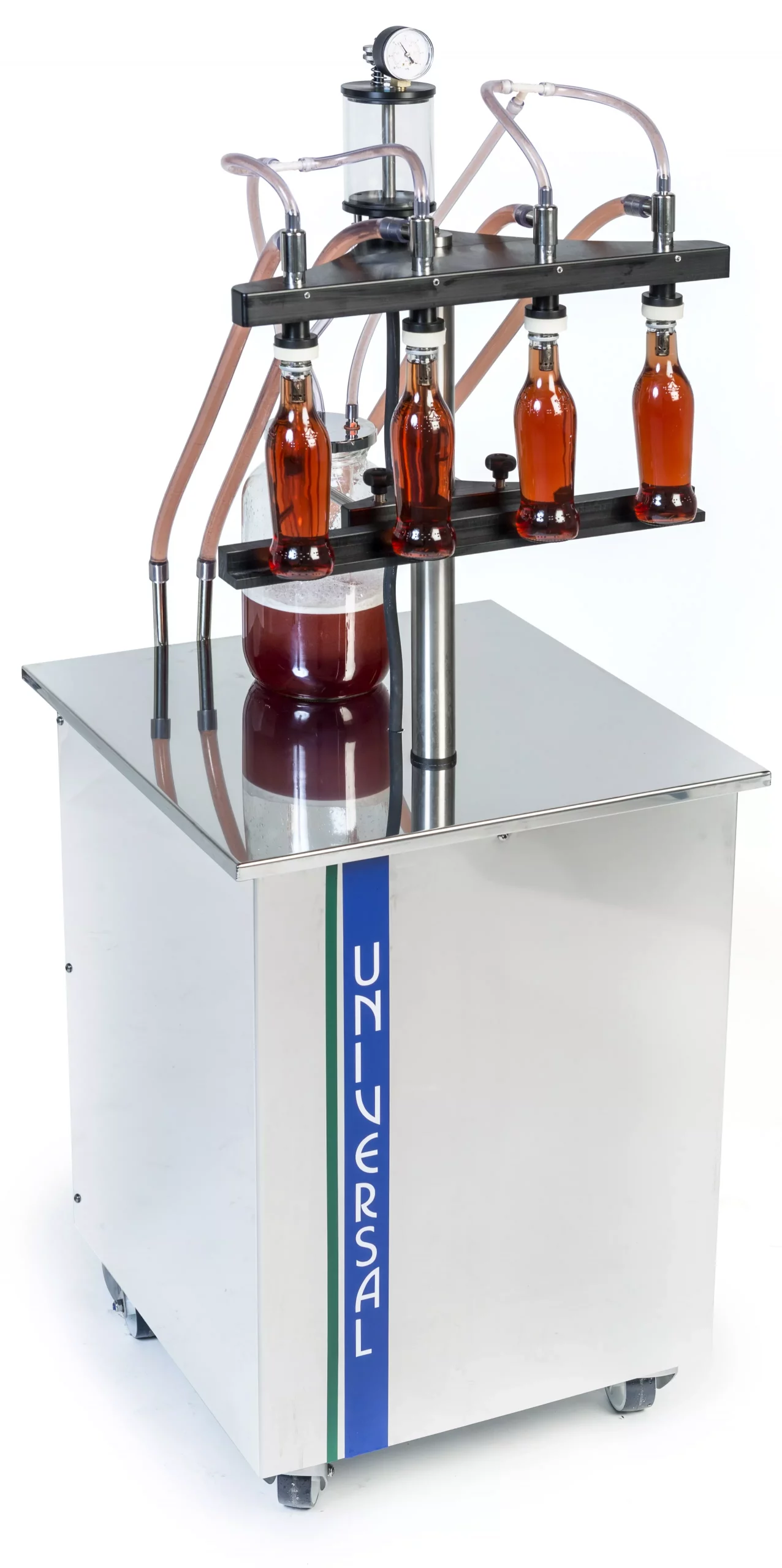
This airtight seal creates a vacuum within the bottle which draws free-flowing liquids from a supply tank into the bottle, via specially designed nozzles. These nozzles have a small hole on the side which is connected to a small internal tube.
The height of this hole in relation to the top of the container during filling determines the level of liquid dispensed. The small hole in the nozzle scavenges excess liquid from the filling process and collects it in a receiver for reuse.
Vacuum level filling machines fill containers to the same height each time, rather than dispensing the same volume. This is particularly useful for glass bottles which will be side-by-side on display shelves in shops. Glass bottles vary in capacity quite a lot, yet vacuum-level filling ensures the level each bottle is filled to is the same, giving a consistent appearance from one bottle to the next. Vacuum level filling requires rigid containers which won’t collapse under a vacuum.
Vacuum-level machines have virtually no moving parts, making them incredibly reliable, and can fill up to 120 bottles per minute depending on the container type, number of filling heads and level of automation.
Bottles are simply positioned with their top in contact with a sealing ring around the nozzle. The container will start to fill as soon as an airtight seal is made and stop when the pre-determined fill height is reached.
There are several advantages of using an automatic bottle filling machine for liquid filling compared to manual or semi-automatic methods.
Here are some key factors to consider:
- Increased production efficiency: Automatic bottle filling machines can fill a large number of bottles quickly and accurately, improving production efficiency and reducing the time required for filling.
- Consistent filling accuracy: Automatic filling machines use precise measuring systems to ensure that each bottle is filled to the exact same level, ensuring consistent product quality and reducing product waste.
- Reduced labor costs: Using an automatic filling machine eliminates the need for manual labor, reducing labor costs and allowing workers to focus on other tasks.
- Flexibility and versatility: Automatic filling machines can be customized to accommodate different types of liquids and bottles, making them versatile for use in a wide range of industries and applications.
- Improved safety and hygiene: Automatic filling machines are designed with safety features to prevent accidents and ensure the safety of workers. They are also easy to clean and sanitize, improving hygiene and preventing contamination.
- Reduced product loss and waste: Automatic filling machines are designed to minimize product loss and waste, which can help to reduce production costs and improve profitability.
An automatic bottle filling machine can offer significant advantages for liquid filling in terms of production efficiency, accuracy, cost-effectiveness, safety, and product quality.